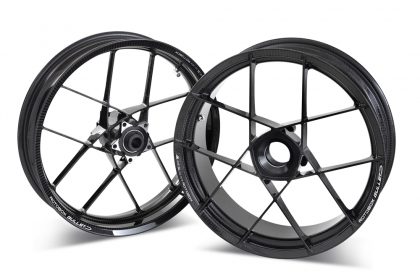
Rotobox Carbon Fibre Bullet Wheels Official UK Dealer
Thank you for visiting our online store.
We are official UK dealers for the awesome and unique Rotobox carbon fibre wheel manufacturer.
Below is info about each wheel they manufacture, to shop for wheels for you bike click on the link below:
CARBON FIBRE FEVER
Low weight, high stiffness, great strength and eye-catching design are the obvious reasons for the continuing growth of carbon fibre used in the motorcycle industry. One of the most important parts to significantly improve a motorcycle’s overall performance – from handling, breaking to acceleration – are carbon fibre wheels. With the industries first 3 component composite (carbon-epoxy-steel) and its unique one-piece hollow carbon cast construction, Rotobox is redefining the quality and manufacturing standards of a whole industry. This puts us on the forefront of carbon fibre motorcycle wheel innovations.
ONE-PIECE HOLLOW CARBON CAST
Rotobox is the first and still the only carbon fibre motorcycle wheel producer in the world to develop and use a unique 3 component composite – combining carbon, epoxy and steel. As the composite itself, the one-piece hollow carbon cast production process is a novelty as well. During production, several different types of CNC tailored carbon fabrics are hand placed into the negative forming mould of the high precision aluminium tool. For greater impact resistance a stainless 2,5 mm steel wire is added in each side of the rim. Next, the liquid epoxy resin is injected into the sealed and tempered tool under very high pressure. This process of producing the one-piece hollow carbon cast is an adaptation of the special high-pressure Resin Transfer Molding (RTM) technology. Ensuring the continuous quality, safety and accuracy of the production process.
SOLID THIN SPOKES
To create solid thin spokes we use special carbon fibre yarn developed for military use. Because of the extreme mechanical properties of the fibres that we use (tensile strength 6000 MPa) and high-density forging process, the cross-section of spokes becomes small and compact.
CHOPPED CARBON FIBERS MEETS WOVEN FABRIC
Our unique technology enables combining chopped carbon fibres with woven fabric seamlessly in the one-piece monocoque.
THE CENTRE PARTS
The hubs are CNC machined from 7075 T6 aluminium alloy, anodized into optional colour and permanently assembled to the carbon rim. Designed specifically for each motorcycle model, the Rotobox wheels are a direct replacement of the OEM-wheels and are supplied with a cush drive, sprocket carrier, spacers and a choice of ceramic or steel bearings.
HIGH-PRESSURE CORE
The new technology achieves a high density of armature in the composite, extreme metric accuracy and a greater smoothness of the wheel surface. In addition – the wheel becomes watertight. Thanks to the High-Pressure Core Technology the structural rib is placed in the inner side between the spokes, with its mission to support the stress hot spot of the wheel. As a result the BOOST elegant spoke design brings greater stiffness and although the spokes are thinner the BOOST is stronger than ever – with a permissible static load of 280 kg on the rear and 180kg on the front wheel
RACETRACK INSPIRED DESIGN
The look of the Rotobox wheels is determined by the company’s philosophy to achieve the highest possible performance and safety with no compromises to popular design guidelines. To maximize the advantages of carbon fibre composite, and simultaneously reduce all known disadvantages, we let the experience and expertise of our professional testing team YART (Yamaha Austria Racing Team) flow into the wheel design. The outcome is a spoke, which meets the rim on a substantially large area.
TESTING LAB
RADIAL FATIGUE TEST
The test aims to confirm the durability of the rims and hubs. For this purpose, a drum is rotating the wheel at a constant velocity of 80 km/h while applying the radial load (FW: 340kg / RW: 560kg at min. 500.000 cycles).
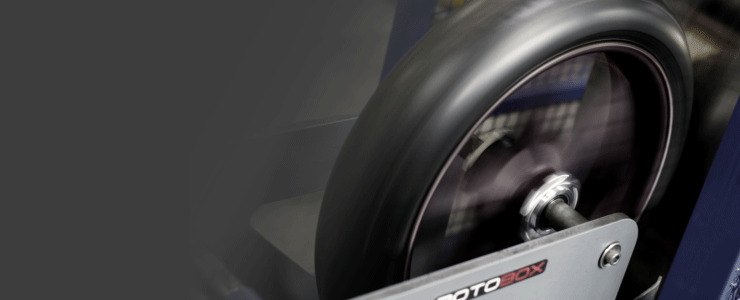
TORSION FATIGUE TEST
The test aims to confirm the durability of the spokes and hubs. For this purpose, the wheel is fixed onto the support, while the torsional moment (FW: 442Nm / RW: 790Nm at min. 100.000 cycles) is repeatedly applied through the contact surface of the hub.
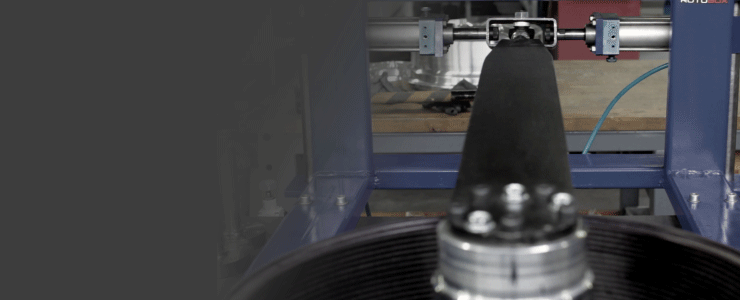
CORNERING FATIGUE TEST
The test aims to confirm the durability of rims and hubs. For this purpose the wheel is fixed to a rotary disc, that is able to provide a bending moment (FW: 217Nm / RW: 387Nm at min. 100.000 cycles) to the centre of the wheel while rotating with a constant velocity.
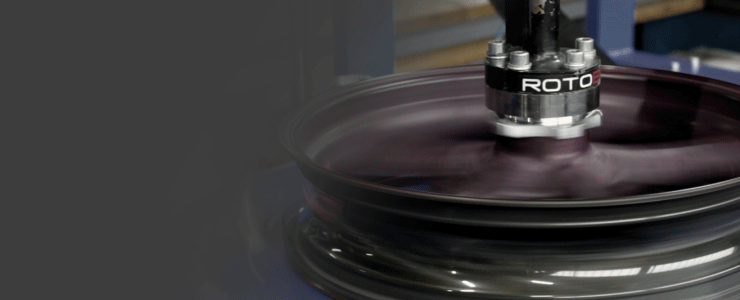
IMPACT TEST
The test aims to confirm the air attainability of the tires and strength of the rims, spokes and hubs. For this purpose, the striker weight (FW: 225kg / RW: 375kg) is dropped on the wheel from a height of 150 mm to apply the impact load.
RACERS KNOW, WHAT RACERS NEED.
How to make the lightest and strongest wheel on the world? That’s the question motorcycling racer, research & development engineer and Rotobox CEO Gregor Bizjak asked himself more than a decade ago. The answer was a revolutionary 3 component-carbon-epoxy-steel-composite and a newly developed production procedure, which paved the way for a new generation of high-performance motorcycle wheels by Rotobox.
THAT’S HOW WE ROLL
Since the very first day, Rotobox strives to take the performance of carbon fibre wheels to a new level. By continuously pushing the boundaries of creative engineering our products set industry standards for lightness, stiffness, design and premium quality. Whether on the track or on the road – the racing DNA of the Rotobox team is not only reflected in our wheels but can be felt with every meter driven. The feedback of our great costumers confirms, that we are turning the wheel the right way.
SIMPLY THE BEST